Learn
Threads of Creativity: Textile Design
Textile designers are the creative minds behind the patterns that adorn our fabrics and garments. Their job involves creating intricate designs and motifs that are then translated onto woven materials. In the past, textile design was a laborious process that involved hand-drawing or painting patterns onto paper or fabric. However, with the advent of technology, the tools and techniques used by textile designers have undergone a significant transformation.
The Jacquard loom, invented in the early 19th century, was a groundbreaking innovation that revolutionized the textile industry. This mechanical loom used punched cards to control the weaving process, allowing for the creation of complex patterns with greater speed and precision. While the Jacquard loom was a major advancement, it still required designers to create physical templates for the punched cards.
The process of making a single textile took countless hours and hands. To start, a designer would create a painted sketch. If you look closely, you can see the hand painted details in many of the designs. These designs would go on to become jacquard loomed or silk screen printed bedspreads.
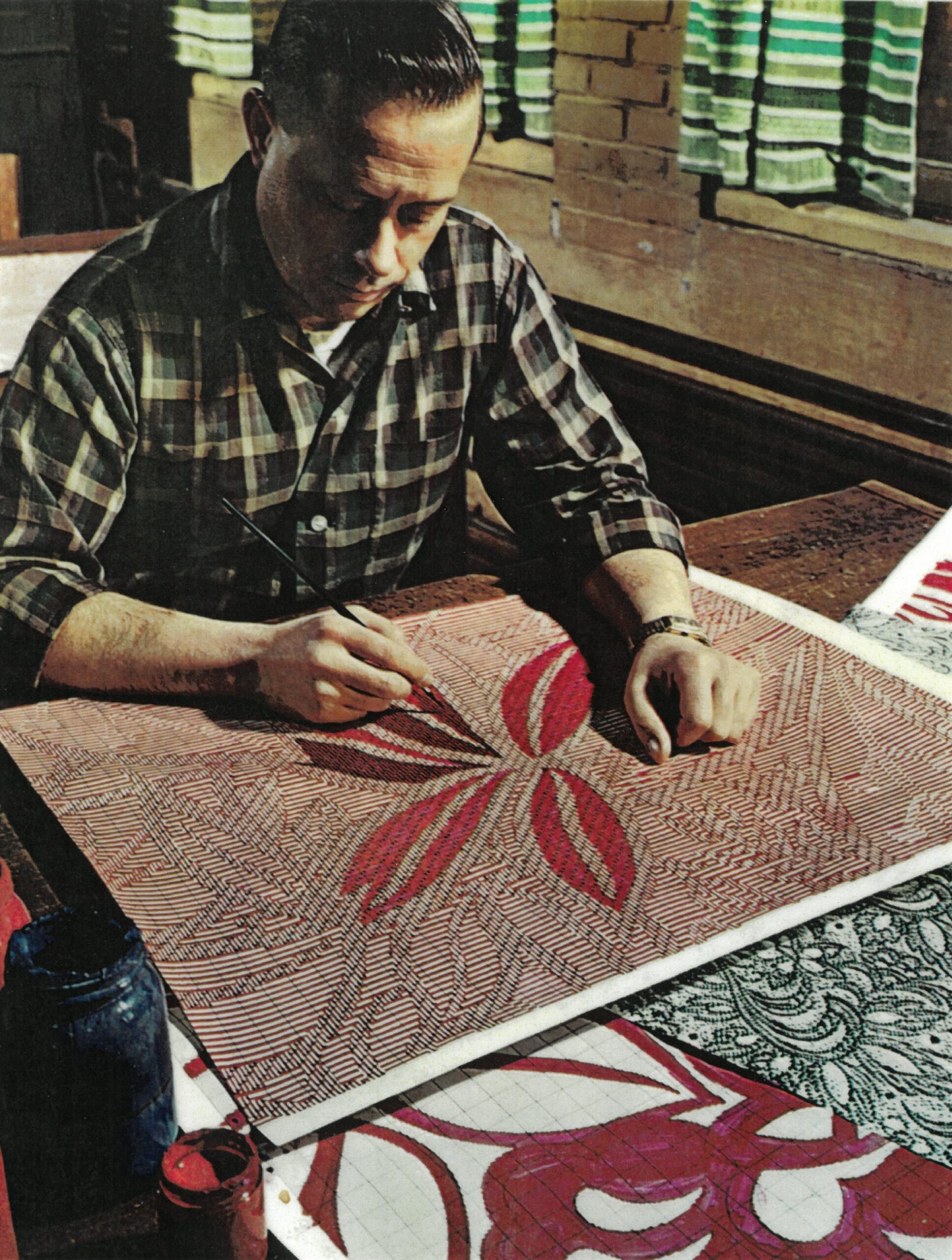
Selected Designs from the Bates Art Department
Pattern to Production
After being edited and approved, patterns for the jacquard loom would be translated onto point paper by someone who hand colored each small square, representing where two threads cross. The paper would then be passed on to a machine operator who translated the pattern onto jacquard punch cards.
If the designs were being screen printed, the final drafts were sent out of house to be transferred onto screens. The Mill would then receive a separate screen for each color used in the pattern. When Bates first started screen printing in the 1960s, it was all done by hand. By 1969, a fully automated, eight-screen printing machine produced 12,000 yards per week.
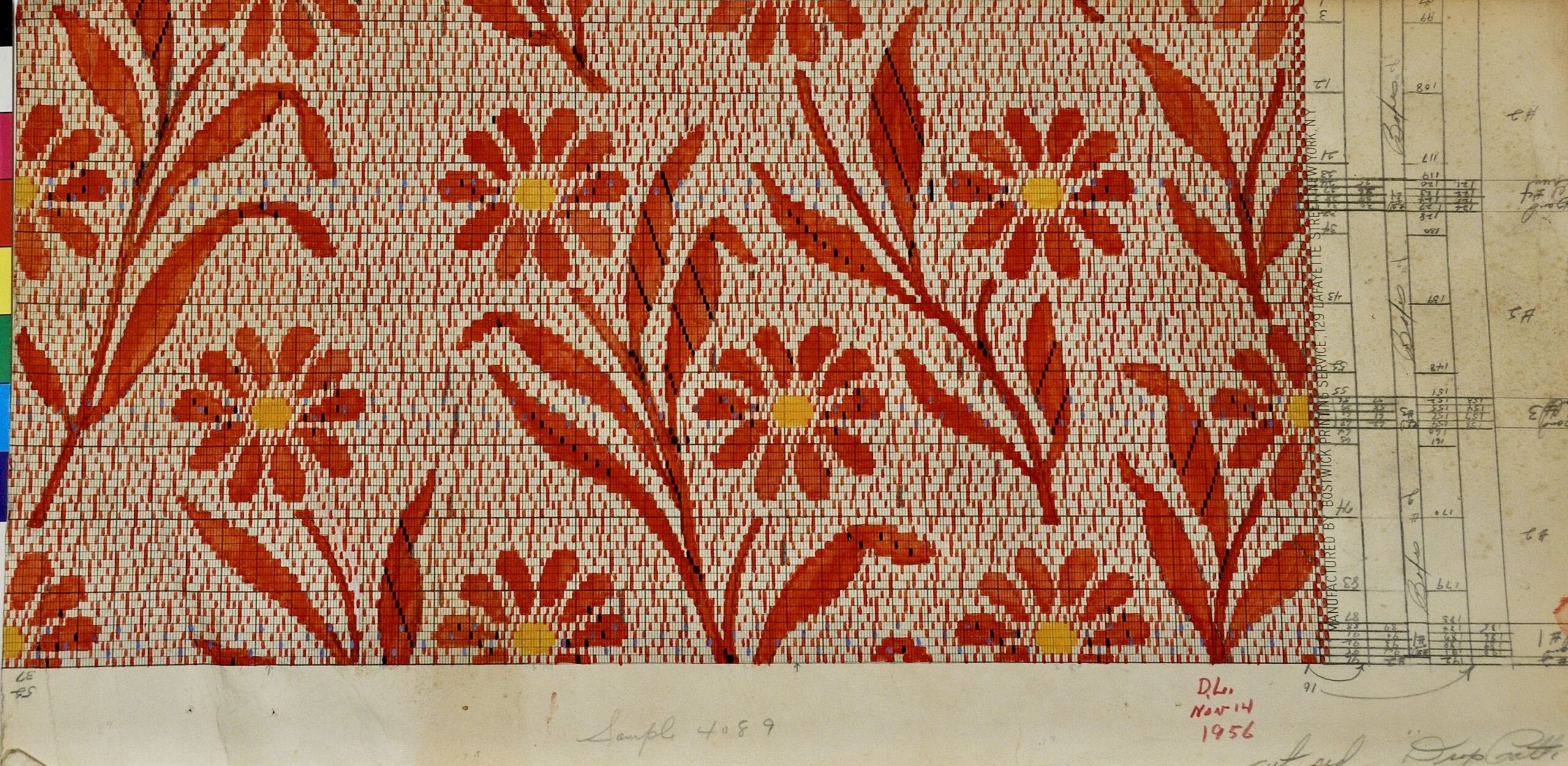
-Ray D’Amour, Bates Designer
“I was a screen printer, and what that entails is setting the machine up to make a design on a bedspread. There may be two screens, there may be four screens, there may be eight screens, and each screen has got a design which coincides to a color of the dye. So when the belt would move over, you had to make sure that the design would intertwine with the other design so that when it came out it would look like one complete design.”
-Danny Fitzsimmons, Screen Printer
Listen to Ray's Quote
Listen to Danny's Quote
Design for Mass Production
The design practice behind the textiles remained innovative and expressive despite the large-scale production. After being given a basic theme, Bates Mill artists often had creative freedom for their design work. The designers who created the patterns had their art distributed across the nation and world. However, their designs were represented solely by the Bates name, leaving the creators themselves largely unknown, despite the fact that their patterns were distributed across the nation and world.
Throughout the history of the Bates Mill, designers painted pattern drafts for each of the textiles manufactured by the company. These designs represent the innovation and creativity at the height of mill production. While Bates bedspreads were manufactured at a mass scale, the designs highlight the individual artistic effort behind the production. Bates Manufacturing Company designers created usable textiles that were beloved by millions of people across the world and passed down through generations.
Textiles with Cultural Connections
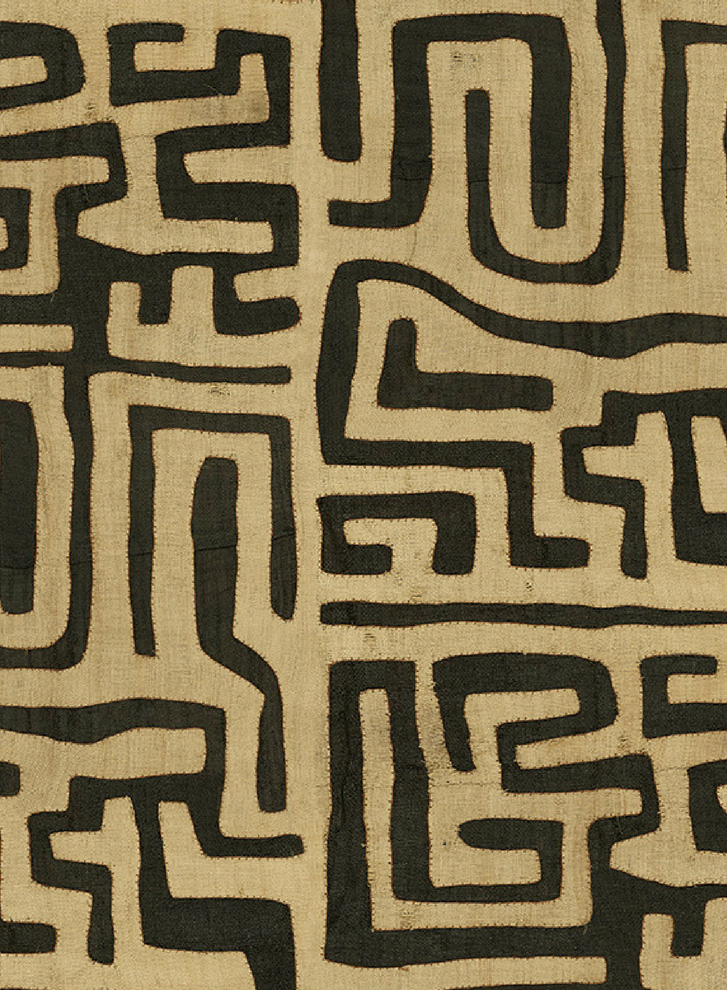
Kuba Cloth
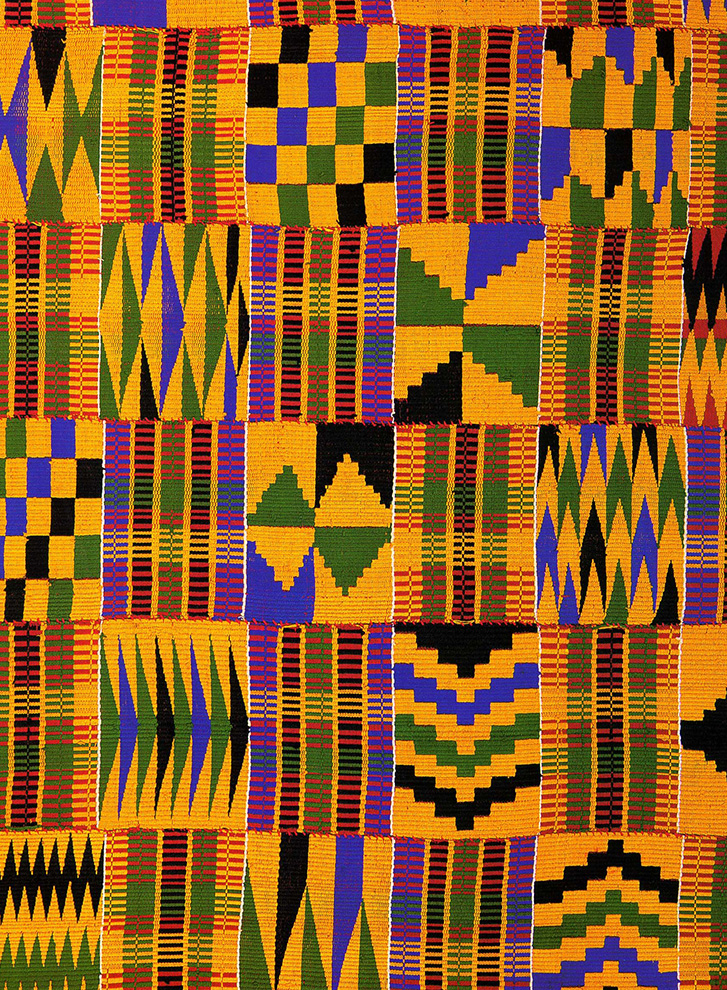
Kente Textiles
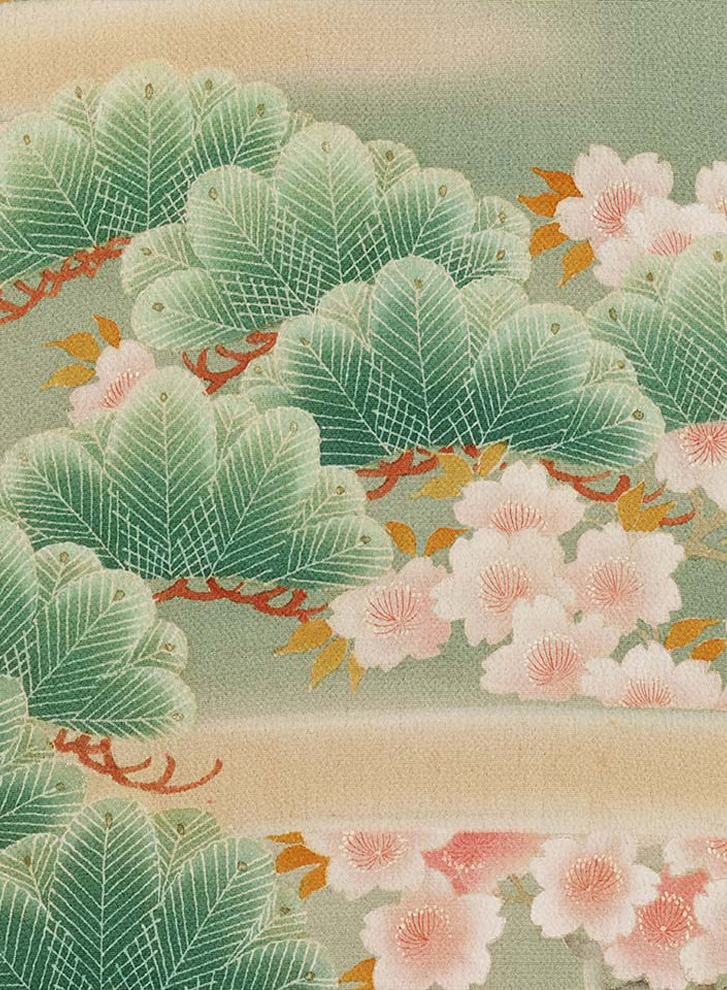
Japanese Textiles

Navajo Textiles
Modern Textile Design
Today, textile designers have access to a wide array of digital tools and software that enable them to create and manipulate patterns with ease. Computer-aided design (CAD) software allows designers to sketch, draw, and color patterns on a digital canvas, offering a level of flexibility and control that was previously unimaginable. These digital patterns can then be directly transferred to computerized looms, streamlining the manufacturing process and reducing the risk of errors.
Digital printing technologies have opened up new possibilities for textile design. Designers can now create high-resolution prints with intricate details and vibrant colors, which can be directly applied to fabric using specialized printers. This has led to a surge in creativity and experimentation within the textile industry, as designers are no longer constrained by the limitations of traditional weaving techniques.
Despite the advancements in technology, the fundamental role of the textile designer remains the same: to create visually appealing and functional patterns that meet the needs of the market. Whether using traditional or digital tools, textile designers must possess a keen eye for color, texture, and composition, as well as a deep understanding of the materials and techniques used in textile production.
Making it in Maine Today:
Modern Textile Design Taking Inspiration From The Past
At Origin in Maine, an ambitious designer and product maker, Pete Roberts, tells his story of linking the past to his present, in the videos below. His team has brought back to life an old loom that was used in the Bates Mill in Lewiston, Maine using it today, to again make textiles in Maine. He and his team honor the heritage of textile-making in Maine and inspire the future of American-made textile products. Check out his Maine-based business: https://originmaine.com